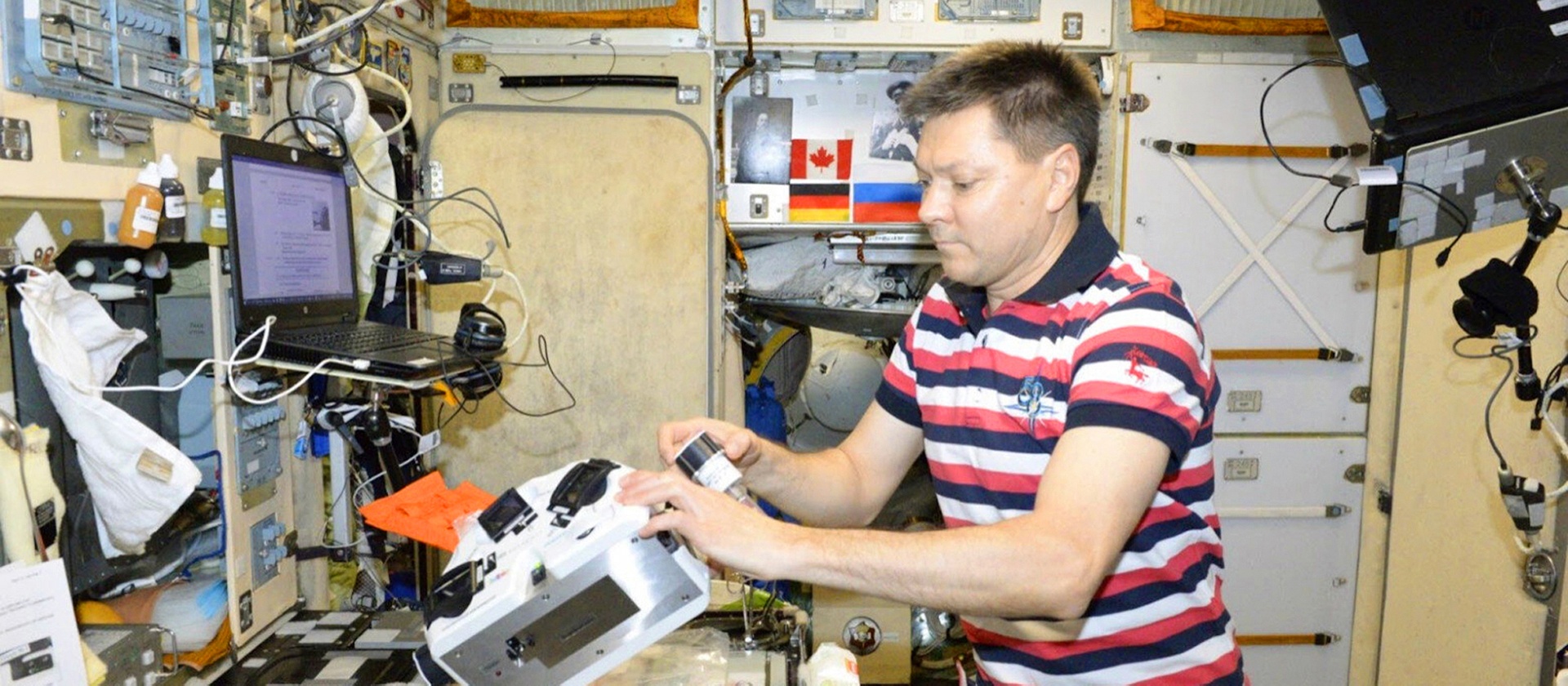
Эта безграничная 3D-печать
«Миром правят знаки и символы, а не слова и законы» — эту мысль приписывают китайскому мудрецу Конфуцию. Скептики шутят: чтобы объяснить мысль, заложенную в эту сакраментальную фразу, надо быть самим Конфуцием. Однако, так или иначе, мысль, озвученная китайским философом, жива и сегодня. Выдержала проверку временем.
Что же можно назвать символами нашего времени, например в оборонке? Их немало. Мне приходит на память, например, символы 5G (пятое поколение мобильной связи) и 3D (трехмерная графика). Если со связью все более-менее ясно — это особый частотный диапазон, то 3D, особенно в сочетании со словом принтер, поначалу ставили в тупик: как можно на принтере создавать объекты и детали для работающих сложных механизмов?
Прежде уточним: изготовление деталей на 3D-принтере напрямую связано с аддитивными технологиями — созданием трехмерных объектов, деталей или вещей путем послойного добавления материала: металла, пластика, бетона и, возможно, в будущем, как утверждают знающие люди, человеческой ткани!
Малошумный самолет
В рамках российской промышленной выставки «Технофорум-2022» состоялся Международный форум по аддитивным технологиям и 3D-решениям «Industry3D». Как видно, два понятия объединены.
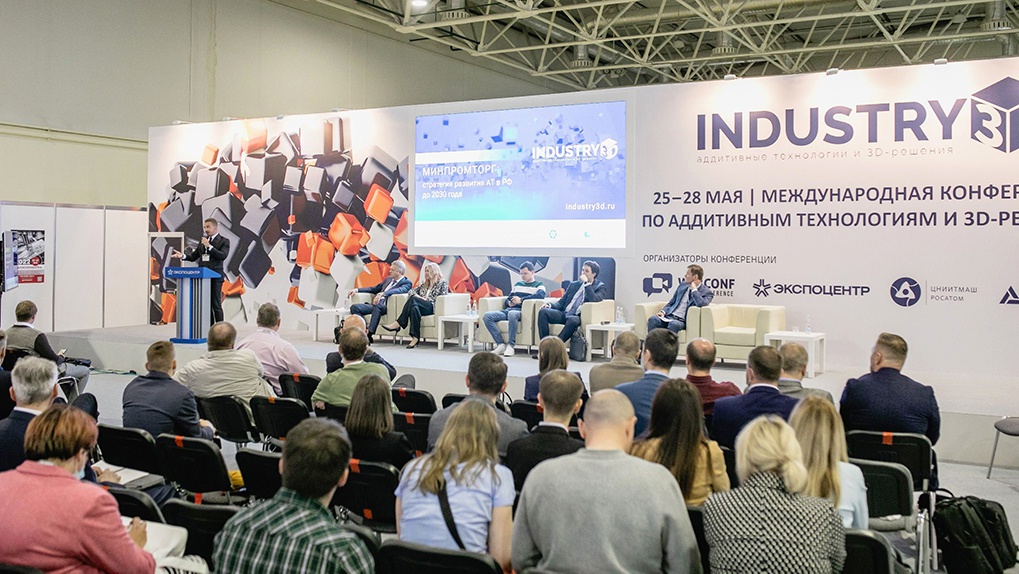
Всероссийский научно-исследовательский институт авиационных материалов (ВИАМ) Национального исследовательского центра (НИЦ) «Курчатовский институт» представил доклад, посвященный разработке материалов и аддитивных технологий для изготовления высокотехнологичных изделий.
В институте, в частности, завершено оснащение ключевым оборудованием аддитивного производства полного цикла. Речь идет о разработке технологий изготовления деталей сложных технических систем, в том числе крупногабаритных, из металлических, металлокерамических, керамических и полимерных материалов.
В интересах ведущих конструкторских бюро авиационной, ракетно-космической и атомной промышленности институт разработал шесть уникальных сплавов и более 30 адаптированных серийных материалов.
Для чего все это делается? Ученые Пермского национального исследовательского политехнического университета выяснили: технология 3D-печати может улучшить свойства звукопоглощающих конструкций авиадвигателей до 20%.
Основной источник шума в самолете — двигатель. Звукопоглощающие конструкции изготавливают в основном из полимерного композита в виде многослойной конструкции. С его помощью самолет можно сделать легче, тише и аэродинамичнее. Но изделия из композитных материалов подвержены дефектам между соединенными слоями. Ученые из Перми решение этой проблемы нашли в технологии 3D-печати.
Рентген экспериментальных образцов показал: детали, созданные с помощью 3D-печати, лучше поглощают звук. Это открытие (без преувеличения) позволило расширить область применения технологии 3D-печати в авиастроении.
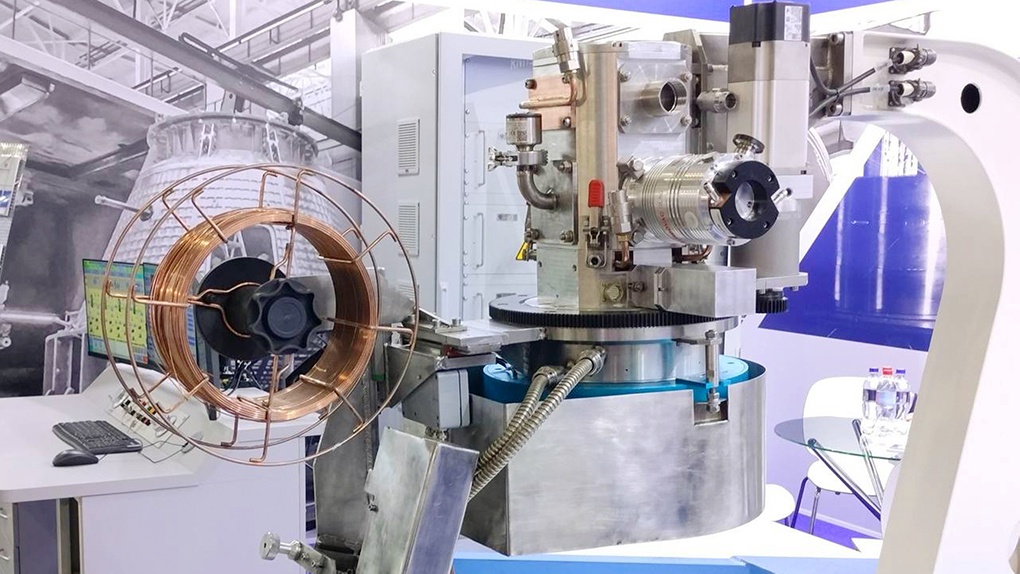
Пермяки изучили дефекты и деформации двух образцов, влияющих на звукопоглощение. Первый изготовлен из полимерного композита воздействием давления и температуры. Второй сделан из ABS-пластика при помощи аддитивных технологий (та самая 3D-печать). Образцы испытали при высоком звуковом давлении — 140 и 150 децибел.
Победил образец, изготовленный при помощи аддитивных технологий. Их совершенствование на основе прочных и легких материалов позволит добиться точной геометрии звукопоглощающих конструкций.
Так вышло, что изготовление деталей с помощью принтера нашло широкое применение в первую очередь в авиакосмическом машиностроении. В госкорпорации «Ростех» создали вакуумный электронно-лучевой 3D-принтер со всеракурсным роботом-манипулятором. Устройство позволяет «выращивать» сверхпрочные детали сложной конструкции из титана и стали.
Для создания сверхпрочных деталей используют специальную проволоку из сплавов алюминия, титана и жаропрочной стали. Всеракурсный робот-манипулятор умеет «выращивать» изделия в условиях вакуума — идеальной среды для получения сплавов с кратно повышенной прочностью. Такая характеристика особенно важна для изделий авиационной и космической отраслей. Показатель предела прочности изделий из нержавеющей стали, к примеру, возрастает на 16%. С помощью 3D-принтера можно получить деталь любой конструкции размером до 2 мм.
Испытания опытного образца устройства планируется завершить до конца 2022 года.
Песчаный принтер
3D-принтер служит не только на земле, но и в космосе. В июне этого года российские члены экипажа МКС на корабле «Прогресс МС-20» испытали прибор на борту станции. Они напечатали 19 образцов: элементы конструкции, лопатки, бюст Гагарина, фигурки шахмат, эмблемы университетов, которые участвовали в эксперименте. Даже штапик для микродрели (потребовали обстоятельства в полете).
Эксперимент по отработке аддитивных технологий производства изделий из полимерных материалов в космических условиях прошел успешно. Космонавты получили возможность в будущем на околоземных орбитальных станциях изготавливать необходимые детали и инструменты в космосе. Не дожидаясь, пока транспортные корабли доставят их с Земли.
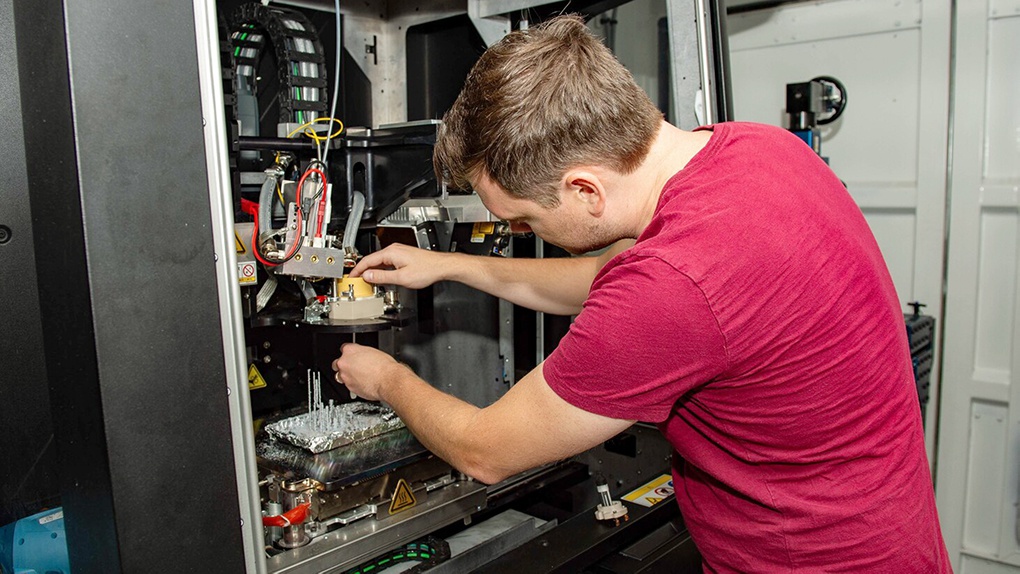
Специалисты утверждают: создание перспективной авиатехники (в частности, самолеты «Суперджет 100» или МС-21 с отечественными двигателями ПД-8 и ПД-14) немыслимо без технологий 3D-печати.
Для изготовления деталей нужно аддитивное оборудование. Его производство освоил Концерн ВКО «Алмаз Антей» на Обуховском заводе. Здесь будут выпускать «Песчаный 3D-принтер» и атомайзер — полностью из отечественных комплектующих.
«Песчаный 3D-принтер» и работать будет на российском сырье и отечественном программном обеспечении. Высокопроизводительная универсальная 3D-машина будет создавать песчаные формы и стержни для сложных отливок. Атомайзер — изготавливать порошки различных металлов и сплавов. Опытные образцы продукции будут готовы в первом квартале 2023 года.
Кстати, Обуховский завод уже производит высокотемпературную аддитивную установку «Ларец» для изготовления изделий из конструкционных термопластичных материалов.
Бионический дизайн
Вслед за предприятиями авиакосмического производства технологию 3D-печати приняли на вооружение и другие отрасли. Объединенная двигателестроительная корпорация изготавливает опытные крупноразмерные заготовки.
В итоге отпала необходимость литья такого рода заготовок, изготовления дорогостоящей оснастки для них. Освоение каждой опытной заготовки заняло не более полутора месяцев вместо года, если изготавливать традиционным методом — отливать, а потом обрабатывать специальными станками.
Военно-промышленная компания, разработчик и производитель колесной бронированной техники, некоторые самые сложные детали для унифицированной колесной бронированной платформы «Бумеранг» «откатывает» на промышленном 3D-принтере. Значительно сокращены расходы на производство опытных образцов техники (в частности, не требуется изготовление пресс-форм и штампов), на производство особенно сложных новых деталей требуется меньше времени.
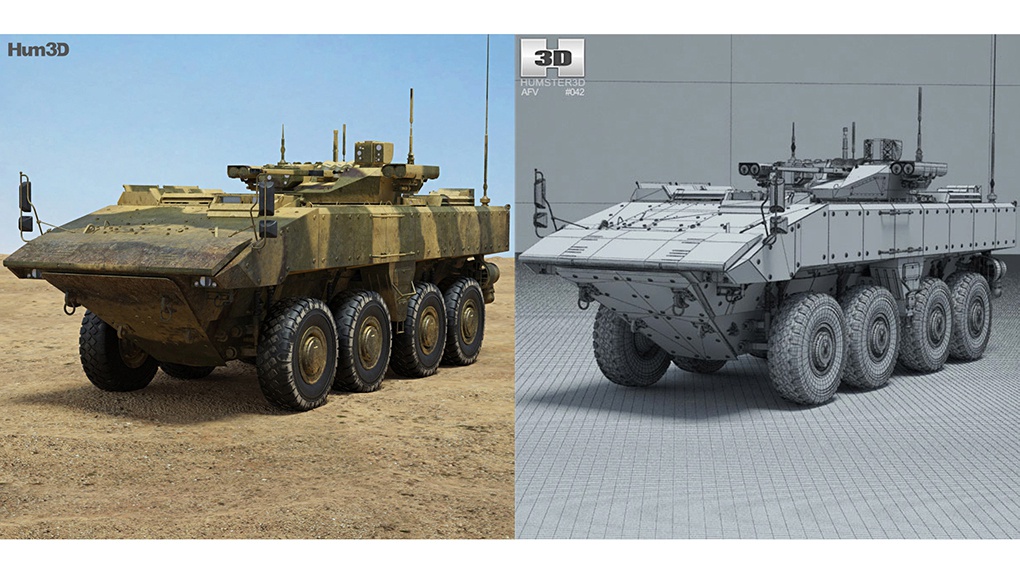
Специалисты Ростеха методом 3D-печати изготовили ключевые детали подвески первого российского беспилотного гоночного электроболида BRT-8D. Уникальность деталей в особом бионическом дизайне и использовании технологии селективного лазерного сплавления (SLM). Изделие получает высокие прочностные характеристики.
Форма изделия спроектирована с применением так называемой топологической оптимизации. Это метод поиска наилучшей компоновки материала при заданных технических параметрах. Бионический дизайн — это когда внешний вид изделия напоминает элементы живой природы. Применяется для проектирования сложных технических устройств и конструкций.
Изготовить бионические детали традиционным методом (с помощью литья и механической обработки) невозможно. Производство подвески с помощью 3D-принтера позволило значительно снизить ее вес, увеличить жесткость, сохранив прочностные характеристики.
Сегодня аддитивные технологии позволяют изготовить любое изделие без ограничений в дизайне, существенно сокращая сроки производства. В том числе, надо полагать, и оружие.
Дефицит специалистов
Технологии 3D-печати широко применяются при изготовлении комплектующих опытных двигателей-демонстраторов ПД-35, ВК-650В и ВК-1600В, корпусных деталей для вертолета «Ансат-М», топливной системы двигателя ПД-14 для лайнера МС-21.
Рост объемов производства таков, что через два-три года может грянуть дефицит специалистов. И Центр аддитивных технологий Ростеха совместно с Московским авиационным институтом внедрили программу подготовки специалистов в этой области.
Набирают для обучения и студентов вузов, и опытных специалистов. Готовят по одной из четырех программ: «Инженер-конструктор по аддитивным технологиям», «Инженер-технолог по аддитивным технологиям», «Онлайн-курс по аддитивным технологиям» и «3D-печать пластиком». Продолжительность обучения от 14 до 30 дней.
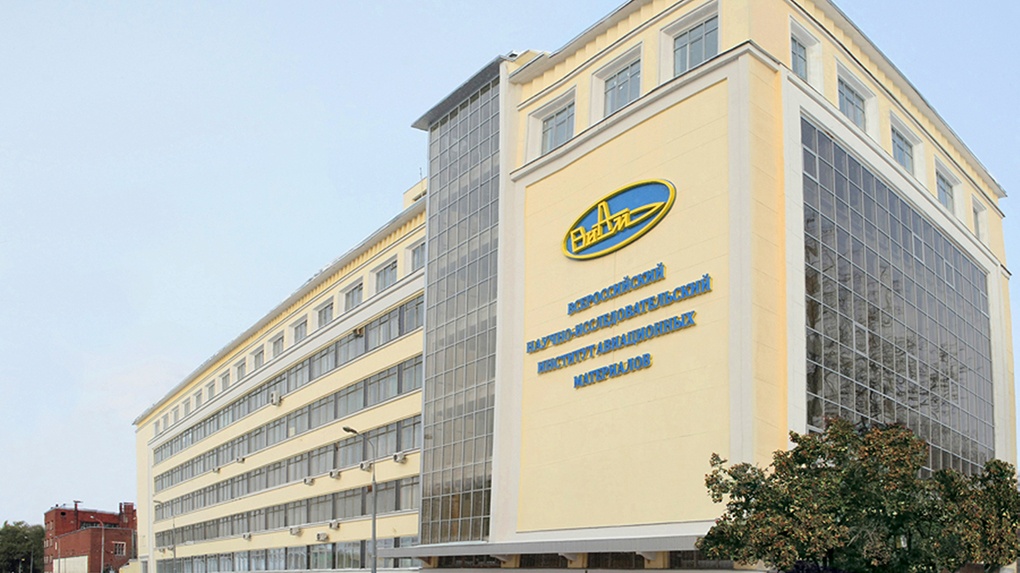
Сегодня нужны специалисты, способные не просто «вырастить» деталь, но и организовать работу по моделированию и топологической оптимизации конструкции, технологическому проектированию аддитивного производства, испытаниям и подтверждению характеристик серийных изделий.
Центр аддитивных технологий Ростеха обладает лицензией Минпромторга на серийную 3D-печать авиационных изделий.
Пять степеней свободы
Разумеется, не только мы пионеры в использовании 3D-принтеров и аддитивных технологий. Передовые зарубежные компании и военные структуры используют и то, и другое весьма активно. Так, командование надводными силами Тихоокеанского флота США установило 3D-принтер даже на десантный корабль USS Essex. Принтер на борту — это возможность не брать с собой в дальние походы большое количество запчастей: мало ли что может случиться.
Да, на борту USS Essex есть мастерские, где можно изготовить некоторые мелкие детали. Однако принтер дает возможность быстро напечатать любую самую сложную запчасть. А это повышает автономность корабля и его боевые возможности.
Отечественные оборонщики стараются не отстать. Иногда уходят далеко вперед. Вот на волгоградском предприятии «Стереотек» в этом году запустили первое в мире уникальное производство уже 5D-принтеров! Тем самым заметно продвинулись в импортозамещении деталей для работы промышленных предприятий. Проектная мощность «Стереотек» 960 принтеров в год.
Большинство станков предприятий отечественного оборонно-промышленного комплекса — импортные, поставки некоторых запчастей прекращены. Производство их с помощью нового оборудования позволит работать бесперебойно. Планируется запустить пять производственных контуров. Изготовленные на 5D-принтерах детали вчетверо прочнее, чем те же изделия, сошедшие с линий 3D-печати. Детали изготавливаются быстрее, снижена их себестоимость.
Ключевая в новом производстве — пятиосевая машина. Она позволяет наклонять и вращать деталь при изготовлении. А оригинальное отечественное программное обеспечение позволяет подготавливать детали к печати.
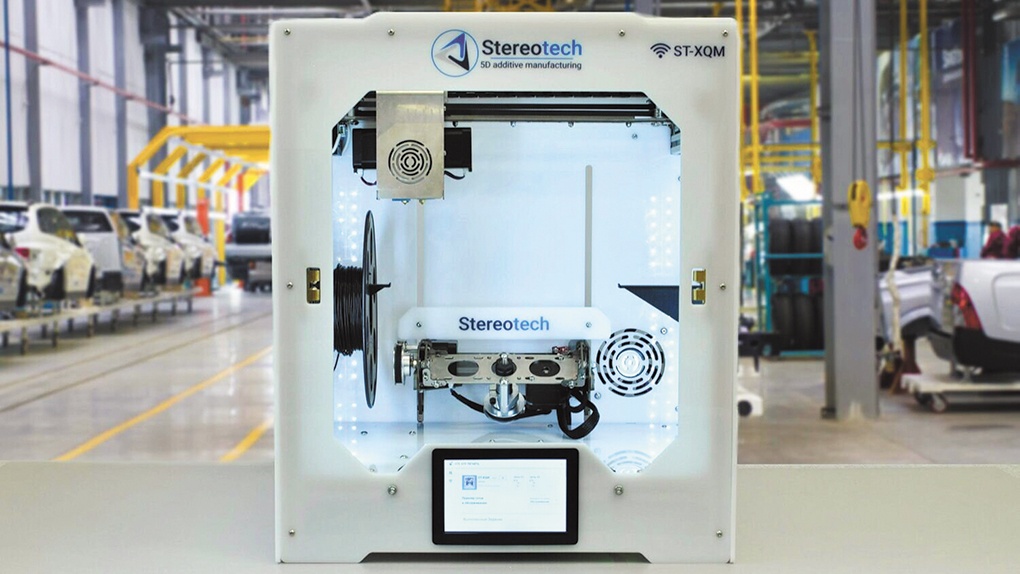
Уже ведутся переговоры на поставку 5D-принтеров за рубеж, в том числе в Китай. В 2021 году компания «Стереотек» получила международный сертификат в соответствии со стандартами Евросоюза. Успели до известных событий.
Гибридный 5D-принтер «Стереотек» для печати более объемных и прочных деталей в работе использует пять степеней свободы. Способен печатать детали не из плоских слоев, как в 3D-принтере, а построенные по сложным пространственным траекториям. Уникальность разработки в режиме печати: упрочнение изделия проводится в объеме как внутри, так и снаружи. Это обеспечивает изотропию — одинаковость физических свойств во всех направлениях — и увеличение прочности на изгиб изделия в четыре раза.